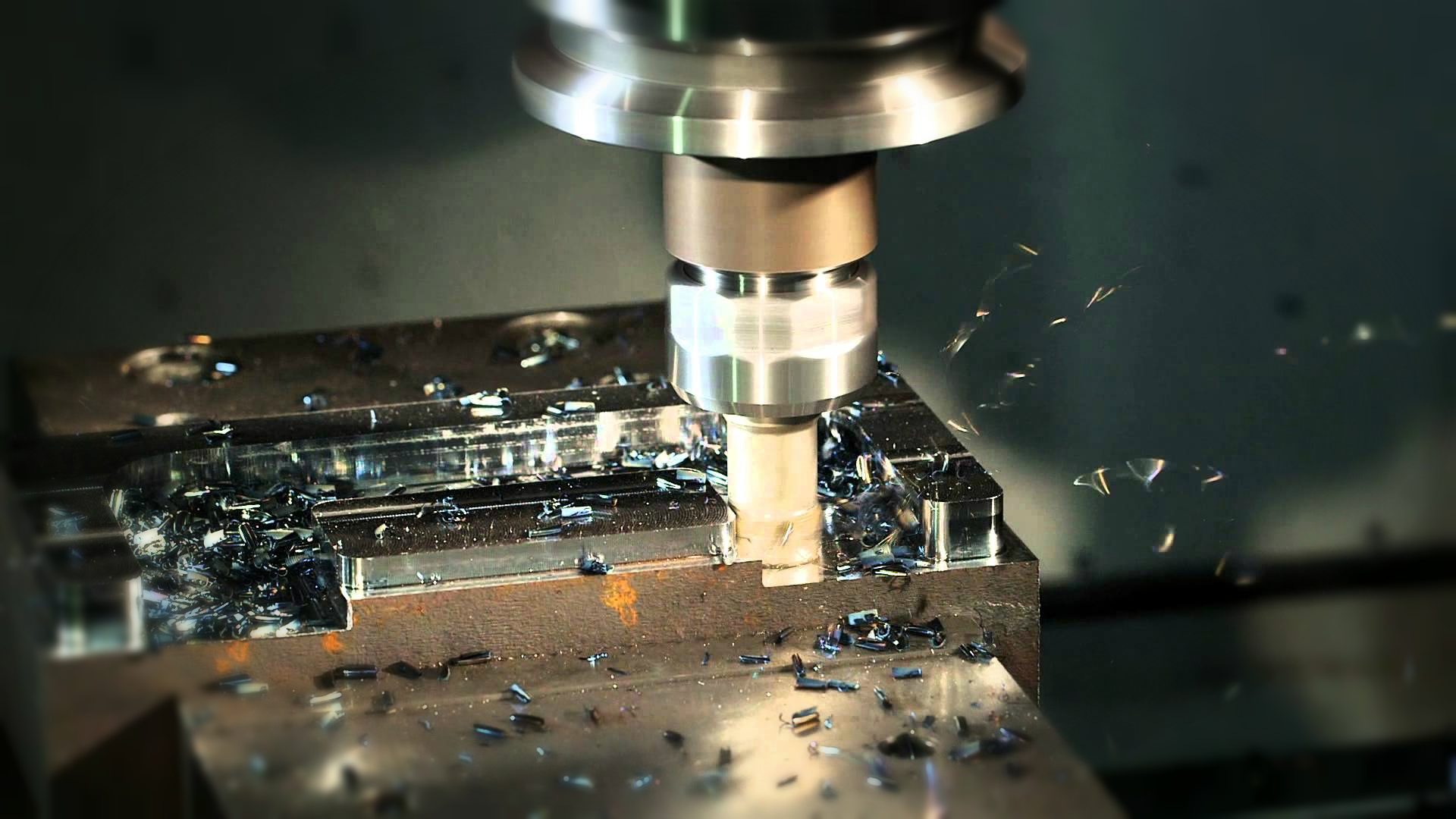
Важным аспектом развития производства является внедрение высокоскоростных технологий механической обработки, что особенно актуально для фрезерования фасонных поверхностей. Реализация такого усовершенствования осуществляется за счет использования станков, оснащенных системами числового программного управления. При этом минимальная частота вращения шпинделя должна составлять 20 тыс. об/мин, а подача должна находиться в пределах 3-10 тыс. мм/мин. При таких режимах резания особые требования предъявляются как к самой мехобработке, так и к оборудованию на которой она производится, а также к металлорежущему инструменту.
Высокоскоростная обработка (ВСО) — это прогрессивная технология. На сегодняшний день она применяется на промышленных предприятиях разных стран мира с целью изготовления:
- пресс-форм из стали, алюминия, оргпластики — автопромышленность;
- фольгированных печатных плат — электронная промышленность;
- алюминиевых высокопрочных деталей — аэрокосмическая промышленность.
Если раньше ВСО не было широко распространено из-за несовершенств систем ЧПУ и металлорежущего инструмента, то сейчас подобных проблем не существует. Именно поэтому сейчас наблюдается тенденция динамичного развития технологий ВСО.
Сущность ВСО
Исследования, проведенные в отношении механообработки на высоких скоростях, показали, что образуемая в ходе работ теплота отводится вместе со стружкой (75 процентов), с инструментом (20 процентов) и с заготовкой (5 процентов). Технология ВСО характеризуется возможностью резания при надкритических колебаниях. Более того, в процессе ее реализации возникают небольшие силы резания, за счет чего улучшается точность обработки и качество обрабатываемой поверхности, исключается дробление металла. Именно поэтому ВСО отлично подходит для механической обработки тонкостенных деталей.
Специфическими особенностями ВСО обуславливаются требования, предъявляемые к конструктивному исполнению металлорежущих станков, на которых планируется производить обработку. Это касается не только узлов оборудования, но и систем, отвечающих за его функционирование. В целом, все требования сводятся к следующему:
- оборудование должно обладать хорошей жесткостью и виброустойчивостью, а также демпфирующими свойствами. При этом особое внимание концентрируется на направляющих, ведь все перемещения частей станка должны быть плавными;
- оборудование должно обладать термической стабильностью, то есть деформации, вызванные повышением температуры, должны быть минимальными. Соответственно, тепловое расширение играет одну из главных ролей в качестве мехобработки. Для решения этой проблемы современные станки оснащаются специальными системами охлаждения. Уменьшить тепловые деформации можно и другим способом: заменив определенные металлические детали изделиями из натурального гранита или минералокерамики.
Для изготовления, к примеру, штампов, шпиндель должен вращаться с частотой как минимум 20 тыс. об/мин, а подача должна быть не меньше 3 тыс. мм/мин. В таких условиях механообработки нужно позаботиться о наличии быстрого ускорения/замедления подачи, а сделать это возможно посредством уменьшения массы и инерции движущихся узлов оборудования. Лучший вариант — замена роторного электродвигателя линейным, который способен обеспечить большое значение подачи, высокую точность и бесступенчатое регулирование.