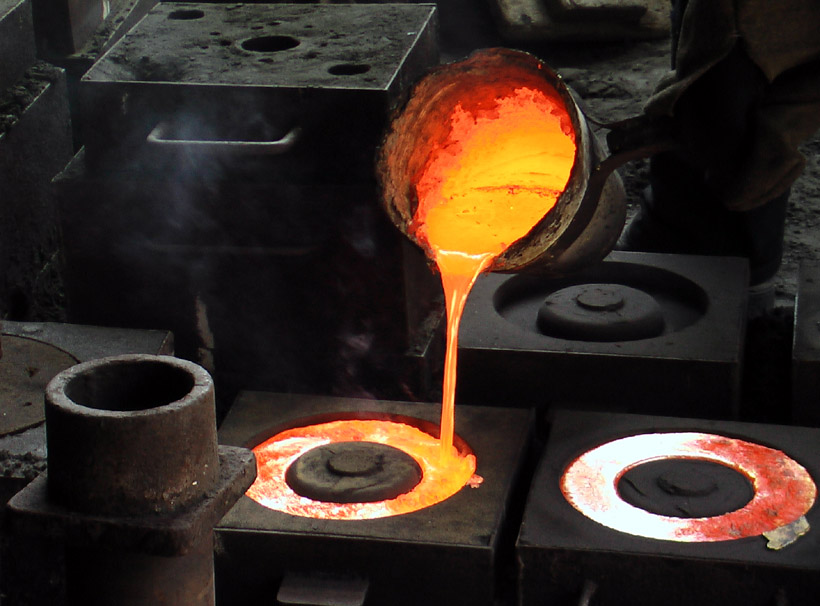
С момента возникновения литейного способа получения металлических деталей минуло без малого почти 7000 лет. Но в промышленных масштабах этот способ стал применяться примерно с середины 17-го века.
Стоит отметить, что во все времена литье отличается большим разнообразием технологических приемов. И во все времена процесс состоял из 4-х основных этапов:
Плавка металла;
- Заполнение жидким металлом формы;
- Извлечение твердой детали;
- Окончательная механическая обработка.
В настоящее время почти половина всех фасонных деталей и заготовок промышленного оборудования, автотранспорта изготавливаются путем отливки.
Литье применимо в изготовлении деталей, применяемых в сложных механизмах, обеспечивающих деятельность автомобилей, оборудования и т. д.
Варианты использования литых деталей:
- Двигатели внутреннего сгорания;
- Блоки цилиндров;
- Поршни;
- Рабочие колеса насосов;
- Газовые турбины:
- Станкостроение
У этого метода есть два ощутимых плюса. Во-первых, существуют большие возможности в изготовлении самых разных деталей. Технология позволяет получать заготовки, изделия самых замысловатых конфигураций. Ни штамповка, ни ковка, ни, даже, сварка такой возможности не предоставляют. Во-вторых, экономичность. Конечная продукция оказывается дешевле по стоимости в сравнении с деталями, произведенными другими способами.
На современном этапе процесс литейного производства подвергся значительной модернизации и реконструирован. Устаревшее оборудование оказалось на «свалке истории». На смену «молоту и наковальне» пришли литейные автоматы и комплексные робототехничесие установки. Разработаны способы высокоточного литья, значительно снижающие отходы производства.
За счет применения высоколигированной стали и высокопрочного чугуна в качестве сырья существенно снижена материалоемкость процесса. Современные плавильные агрегаты «обязаны» обеспечить нужную температуру перехода металла в жидкое состояние. При этом важно добиться минимального расхода топлива, энергии и угара металла. С этой задачей прекрасно справляется индукционная печь, считающаяся самым экономичным вариантом плавильного производства.
Формы для литья в случае небольшого тиража продукции формируются из смеси песка, глины и воды. Если производство деталей поставлено на поток, то речь может идти о многократно используемых металлических формах.
Если речь зашла о сталелитейном деле, воображение тут же рисует дымящие огромные трубы заводов, бурые воды соседствующих рек, голые стволы деревьев. Никто не спорит: процесс действительно характеризуется огромным количеством выбросов в окружающую среду. Произведя тонну стальных отливок, выбросы составят примерно 50 кг пыли, 250 кг оксидов углерода, 2 кг оксидов азота и серы, а также всевозможные фенолы, формальдегиды, цианиды и др. вредные вещества. Особую опасность представляют выбросы при выплавке цветных металлов.
Проблема экологического загрязнения решается очень действенным способом. На отличившиеся в «грязном» деле предприятия накладываются штрафные санкции, что заставляет гиганты по выплавке металлов устанавливать очистные сооружения, внедрять новые безопасные технологи производства.